Industrial Maintenance Overview
by Bluemaint
Strategy and key figures
Our business development strategy is in line with the group’s objectives and will ensure steady growth in terms of turnover and profitability, allowing for future investments.
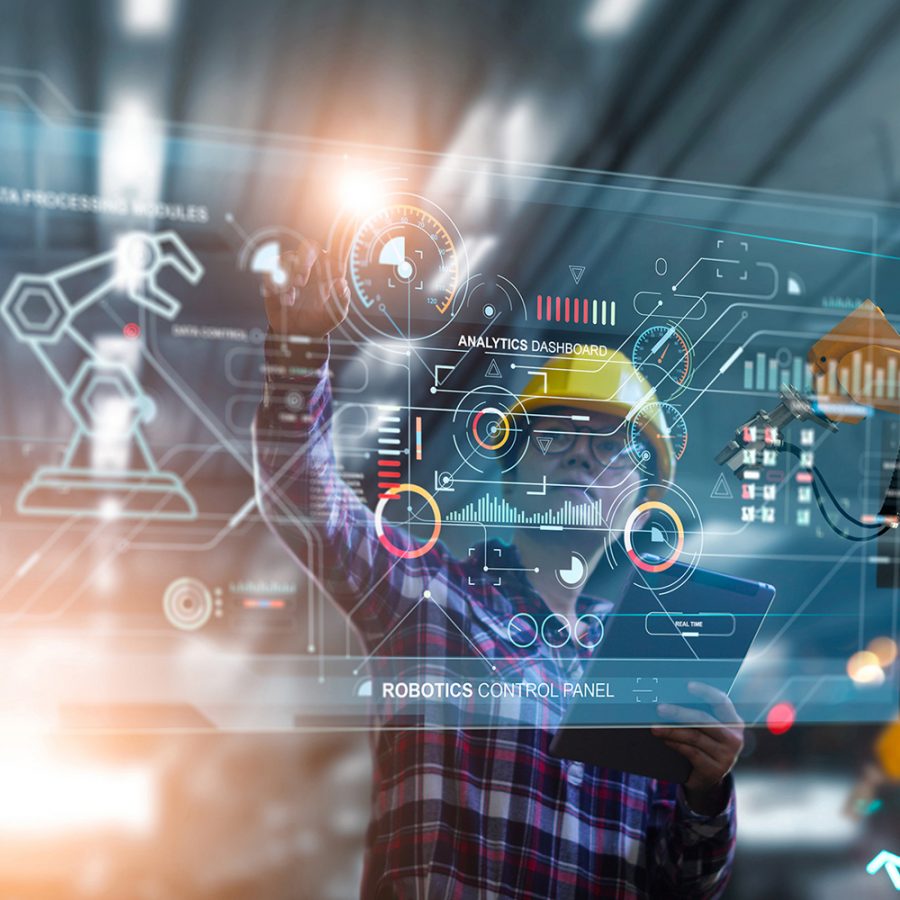
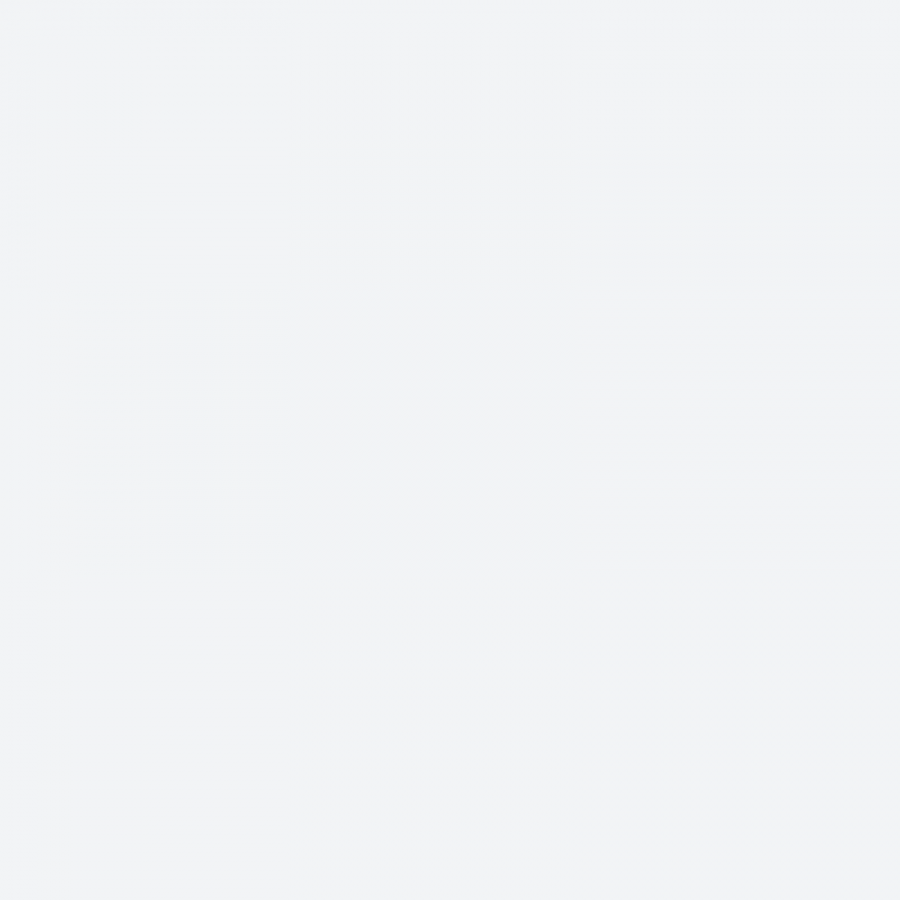
Industrial Equipment Maintenance
An overview of industrial equipment maintenance and condition monitoring
Industrial equipment maintenance plays an integral role in the daily operation of any multi-functional facility. At the highest level, industrial equipment maintenance is a strategy that involves monitoring, inspecting and correcting any issues that can occur with plantwide equipment or systems.
As industrial systems evolve, the implantation of condition monitoring and its required technology (i.e. sensors reporting real-time equipment status and output data) is crucial. With a proper industrial equipment maintenance strategy in place, you can increase your ROI by alleviating unplanned production interruptions caused by system failures.
Consistent in our efforts to guarantee the quality of our services

An overview of industrial equipment maintenance and condition monitoring
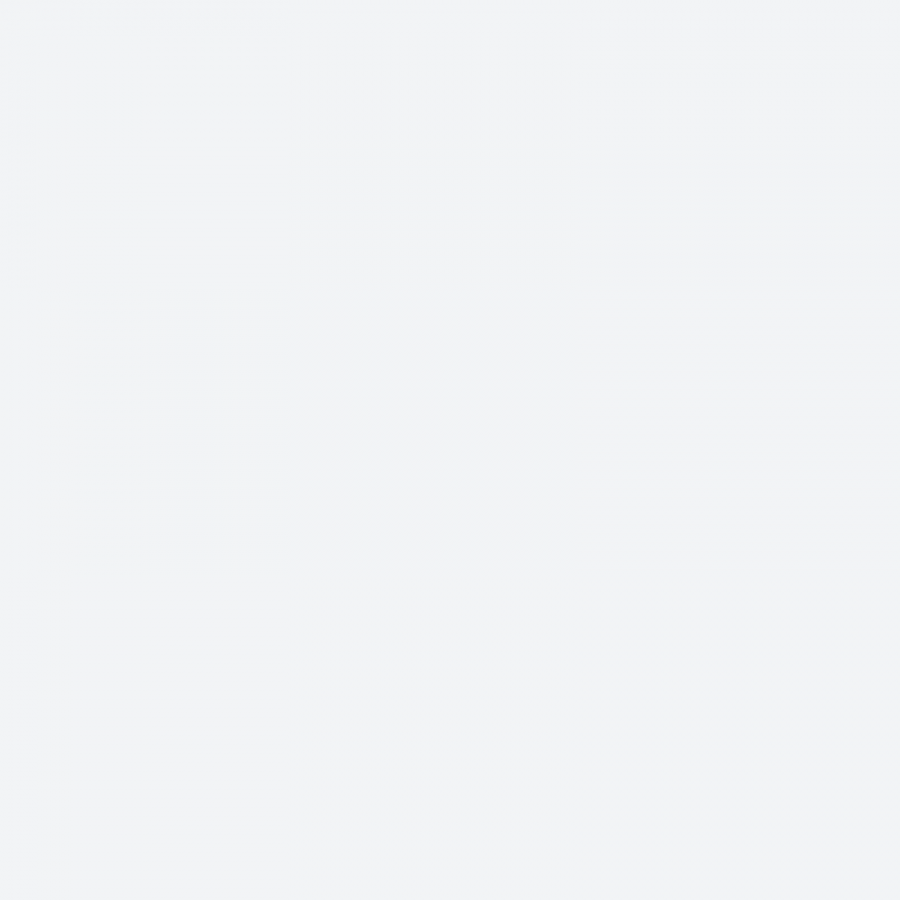
Types of Industrial Maintenance
There are steadfast approaches to developing an effective plantwide maintenance plan. Let’s explore these options further and discover how you can utilize these maintenance methods to achieve optimum equipment performance.
Predetermined Maintenance
Predetermined industrial equipment maintenance is based upon the suggestion of the original equipment manufacturer (OEM). Typically, this type of maintenance is time or calendar-based and relies heavily on a predetermined “wear and tear” threshold. A common example of predictive maintenance would be changing your car’s oil every 10,000 km.
Pros:
- Suggested maintenance and applicable replacement time frames are based on historical data and statistics.
- You can easily automate your scheduled maintenance or replacements so any potential production interruptions can be planned well in advance.
Cons:
- Supplied OEM data is not a “catch-all.” You can potentially risk equipment failures prior to the OEM’s suggested replacement/maintenance date.
- Predetermined maintenance may also be costly if you prematurely replace functioning equipment.
Condition-Based Maintenance
Condition-based industrial equipment monitoring is monitoring the current condition of the equipment to determine a potential risk of failure. This type of maintenance is a predictive maintenance strategy and only occurs when data indicates a performance decline. A common example of condition-based monitoring would be a technician using a sensor to monitor an industrial oven that is not heating up to its intended temperature or taking longer than expected to do so.
Pros:
- This method is cost-effective since maintenance is only performed on an as-needed basis.
- Prevents companies from initiating unnecessary maintenance.
Cons:
- Sensors used can be costly upfront.
- Sensors themselves must be monitored to ensure they are operating properly.
Corrective Maintenance
Corrective industrial equipment maintenance typically occurs when an issue has been during the inspection of another piece of equipment. An example of this type of maintenance would be a plumber noticing and replacing a corroded pipe while on a call to remove a blockage.
Pros:
- This is a cost effective and streamlined process as it does not require additional maintenance strategies or inspections.
- Great for assets that are less critical.
Cons:
- This type of maintenance can be unpredictable as issues are only addressed when noticed.
- Unexpected maintenance on a piece of equipment can cause unplanned production interruptions
Preventive Maintenance
Preventive industrial machine maintenance is the use of scheduled maintenance inspections that are carried out at multiple times each year. A common example would be regularly lubricating the hinges on an industrial oven.
Pros:
- Decrease in equipment downtime or production interruptions
- Life of asset is longer as equipment is regularly inspected and maintained.
Cons:
- Increased cost of time and money to keep equipment maintained
- Potential overuse of resources if a piece of equipment is constantly being monitored when no failure risk is present.
Predictive Maintenance
Predictive maintenance is a form of condition-based maintenance where equipment or operating systems are monitored using attached sensor devices. These sensor devices constantly record data that maintenance technicians use to monitor performance.
Pros:
- An equipment shutdown is typically not required to monitor, so production can continue uninterrupted.
- Constant monitoring will ultimately protect assets from failure.
Cons:
- Condition monitoring equipment can be costly upfront to install.
- It may cost more time and money to train employees to use condition-based monitoring technology correctly.
Modern Pressures of Industrial Maintenance
With slimmer margins and higher cost of complex machinery and processes, industrial equipment maintenance can be a cumbersome undertaking. Ever-evolving regulatory standards require additional resources to keep your systems compliant. In addition, cyber security has increasingly become a threat when using industrial maintenance technology like sensors and other required components to collect real-time performance data. Though it is important to be aware of the modern pressures that accompany industrial maintenance when developing a plan, it is equally important to understand its necessity.
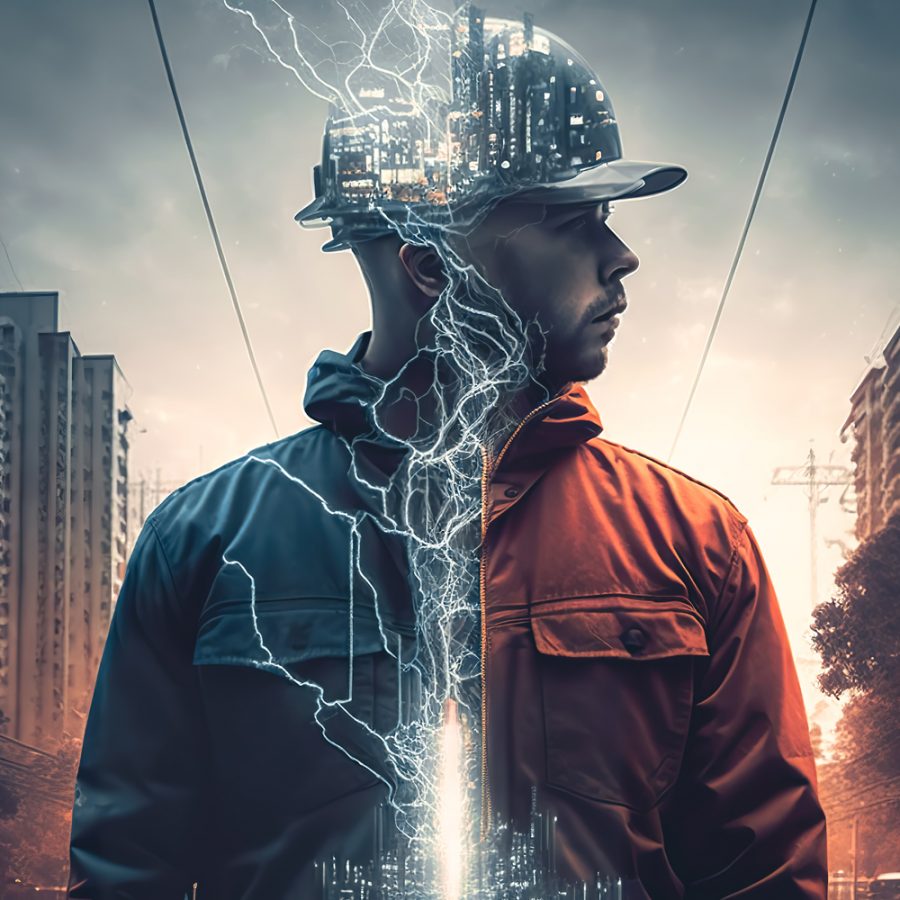
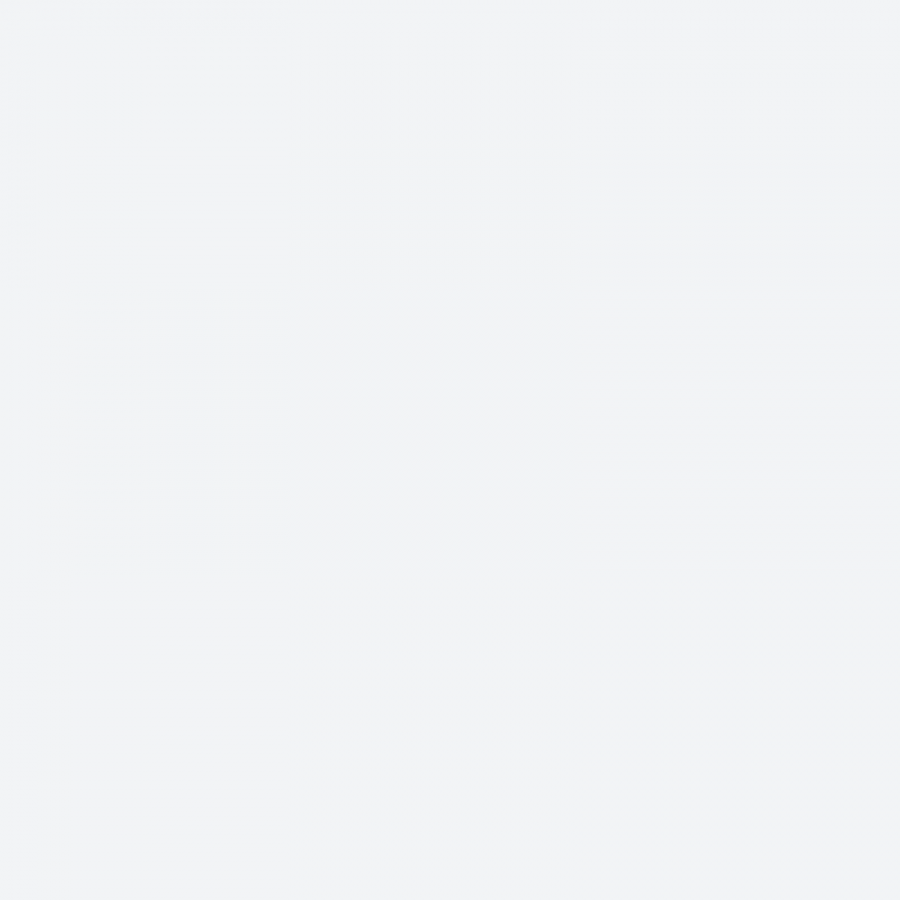
Modern Solutions for Industrial Maintenance - the BLUEMAINT way
The advancement of technology has introduced highly advanced and secure systems, including wireless sensor technology, portable data collection devices, distributed monitoring systems, condition monitoring software and more. We offer several resources and technologies that make it easier and more cost-efficient to develop a well-designed maintenance plan.
The first step in any industrial equipment maintenance plan is to assess both your current operational outputs and future operational goals.
Contact Our Industrial Plant Maintenance Experts For Help With A Customized Plan.
Why Choose Us
Providing you with tailored maintenance services and with our rich industry maintenance experience helps us deliver crucial preventative maintenance to ensure your facilities constantly run smoothly.
All our maintenance, reactive and compliance works are controlled, tracked and transparent to provide you with regular updates on progress. We are here to support you with planned and reactive maintenance. Our engineers monitor every site in order to provide you with fully service, including monthly SLA reports.
We have the resources, equipment and experience needed to maintain sites of all sizes and manage any facilities challenges we face.
What Our Clients Say
Richard Anderson
Seven Media - creative director
Wow! Ut tempus metus dui, non tristique turpis euismod sed. Nulla sed elit faucibus, auctor mauris ac fermentum velit!
Richard Anderson
Seven Media - creative director
Wow! Ut tempus metus dui, non tristique turpis euismod sed. Nulla sed elit faucibus, auctor mauris ac fermentum velit!
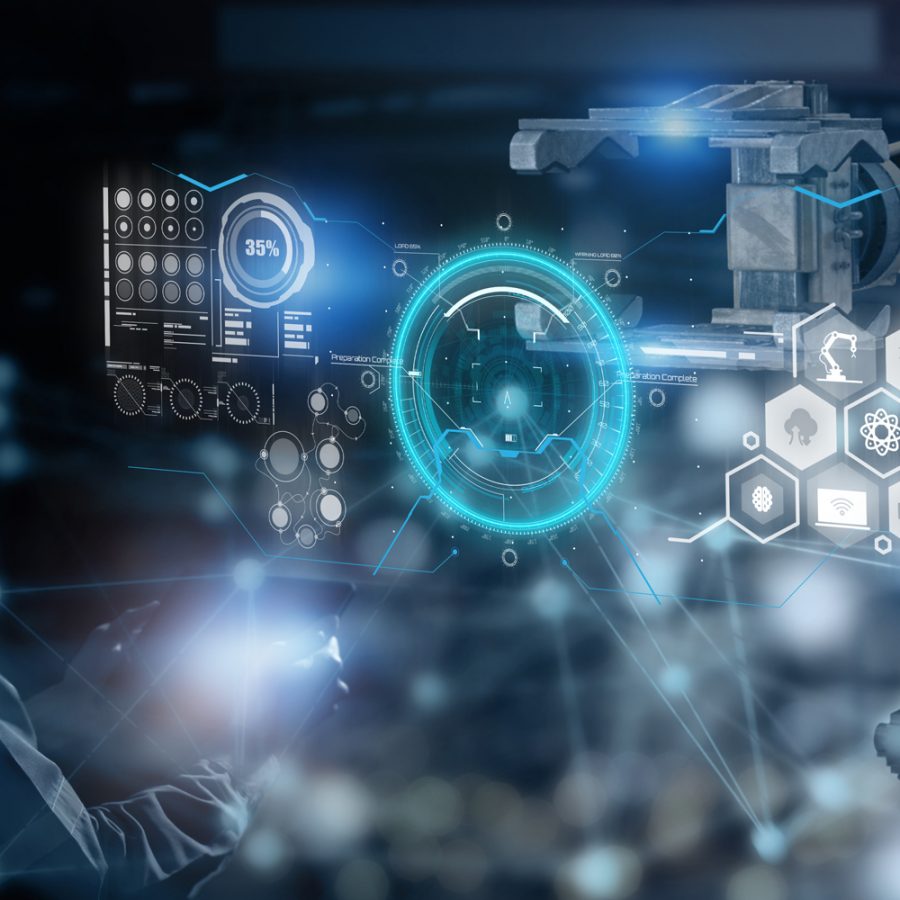
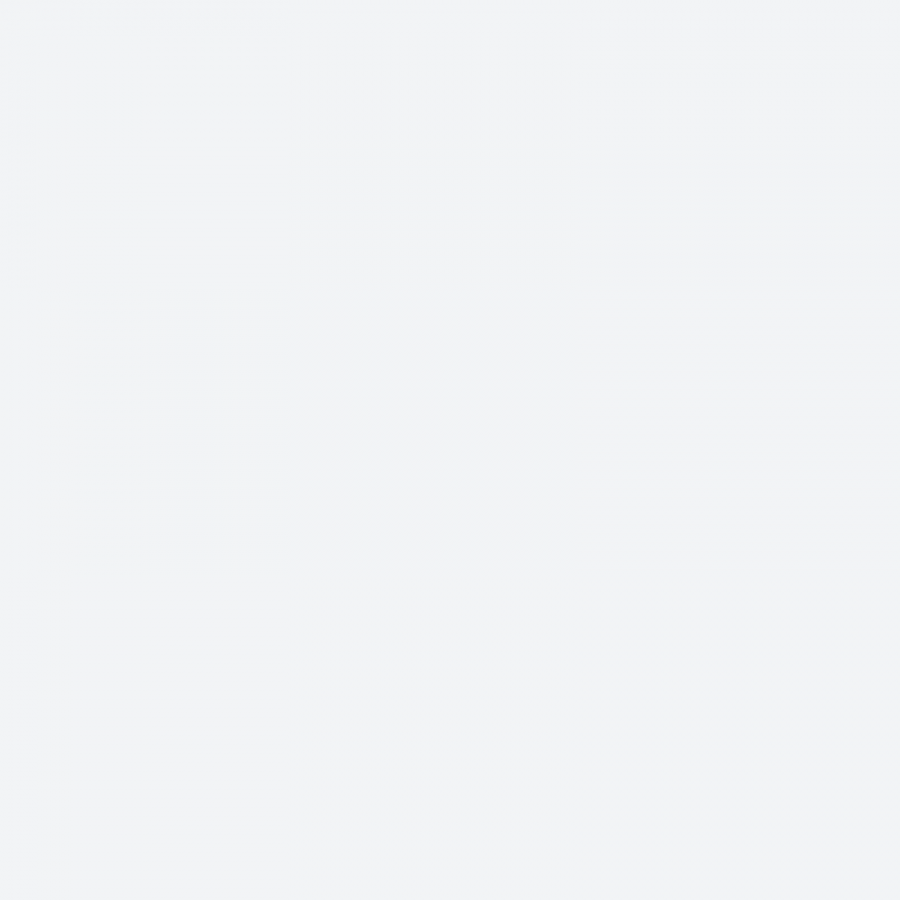